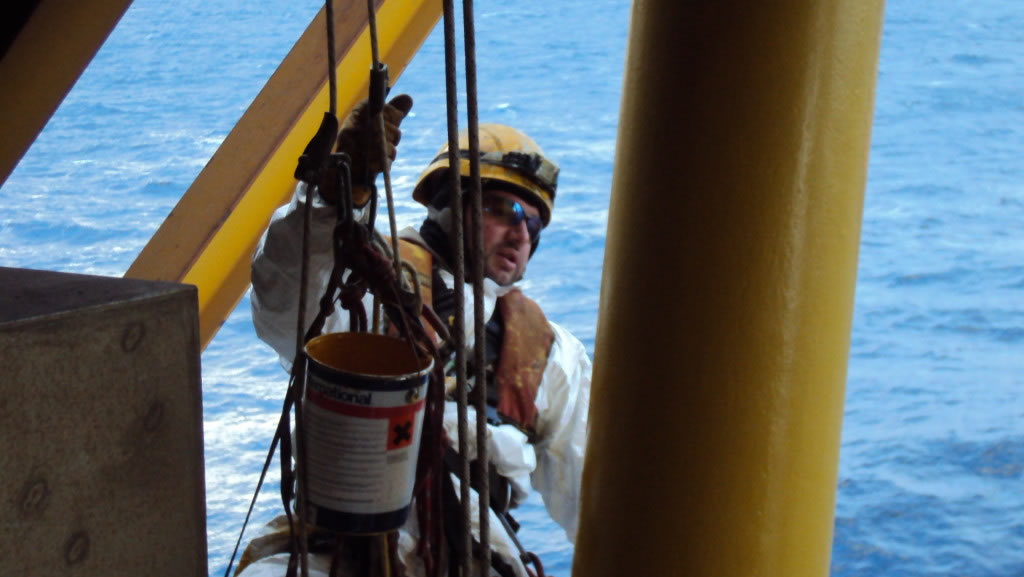
Coatings – The X Factor of Offshore Maintenance?
With asset maintenance and cost reduction the current buzz words for offshore operators in the marine, oil & gas and renewables sector, Matthew Doyle, Commercial Director of NE England-based Wescott Industrial Services explains how investment in coatings repair is a vital yet often overlooked element of preserving offshore and onshore structures.
“Offshore structures are exposed to a variety of harsh environments that are seriously damaging to their protective coatings as well as general operational damage – constant humidity with high salinity, intensive UV light and wave action in splash areas are the perfect conditions for enhanced corrosion. Couple this to limited access and logistical challenges of repair offshore and the ‘perfect storm’ can arise where operators may attempt to postpone coatings repair and renewal, yet they do so at their peril!
In addition, we are now in a situation where several offshore structures, originally designed for a limited lifespan, are now working beyond their planned duration creating severe operational and maintenance challenges, none more so than in their exterior coatings, the first line of defence against critical corrosion. Modern structures, particularly in the offshore wind sector, are now designed and manufactured with far more effective coatings systems, partially due to advanced coatings technology and partially due to an increased awareness from operators of the need for investment in effective coating protection.
Whilst corrosion is inevitable in an offshore environment, it can be controlled by professionally applied engineered coatings systems backed up by maintenance and whilst the cost is considerably greater than similar work carried out in a paint shop at initial manufacture, the cost of no repair or recoating is far greater including catastrophic failure of the structure. The lesson here is very clear – invest in the very best coatings at manufacturing stage and back this up by a regular maintenance schedule.
The story of the painters on the 1.5 mile long Firth of Forth Rail Bridge was factual – the coatings repair work had been on-going since its construction in 1890 leading to the expression ‘like painting the Forth Bridge’. In December 2011, however, the final touches were put to an innovative triple layer of glass flake epoxy paint, developed for the offshore oil industry, on the iconic structure which now won’t need repainting again for 25 years.
The actual coating system or paint used on a typical offshore project is, of course, only a fraction of the total project cost which must include personnel and materials logistics, access systems and safety, lengthy preparation work and increasingly important, environmental considerations. Typical tenders for contracts are now very rarely based purely on cost but take a contractor’s training and safety records and their environmental process for controlling all potential pollution into account.
The modern offshore coating personnel is highly paid and trained, not only in preparation and application techniques but also in securing safe access to their work, whether this be by scaffolding or rope access. Our own company runs regular in-house training courses with all personnel OPITO BOSIET (Basic Offshore Safety Induction and Emergency Training), IRATA and ICATS (Industrial Coating Applicator Training Scheme) certified with supervisors also having the highest Level Three IRATA (International Rope Access Training Association) Rope Access training certification.
Safety is also obviously of crucial importance to operators who rightly judge potential contractors on their record – a recent maintenance campaign which we carried out offshore involved working over 37,000 man hours without a single LTI (Lost Time Incident) on time and within budget which was of crucial importance in winning another contract from our client. This same project demonstrated the importance of environmental factors in that we successfully achieved low emissions by collecting all chippings for disposal and recovering abrasive material when we mechanically prepared the surface for coatings. Another project we have just completed saw us work over 160,000 man hours LTI free over a period of 18 months rectifying damaged fire protection and coatings.
The challenge for the industry is now to address the challenge of structures that are well past their projected life and how to repair and repaint these to extend their working life. Whilst the decommissioning of platforms such as Brent Delta is rightly seen as a huge technical achievement, the challenges of ensuring the integrity of coatings systems on other, equally old, structures will be just as demanding.
Established in 2010, Wescott Industrial Services Ltd work primarily in the Offshore, Transport Infrastructure and Industrial Facilities sectors, enjoying an annual turnover of over £5m and employing some 50 full time managerial, supervisory and multi discipline operatives with the ability to employ temporary onsite crews employed for specific projects to suit requirements. As of 30 June 2017 the company has enjoyed working over 630,000 hours LTI free. The company has their own training subsidiary at Jarrow providing rope access and safety training.